Expert Guide to Casting Aluminum : Methods, Tips & Tricks
Expert Guide to Casting Aluminum : Methods, Tips & Tricks
Blog Article
Opening the Potential of Aluminum Spreading: A Comprehensive Summary
Light weight aluminum casting stands as a keystone in the realm of metalworking, offering a wide range of advantages and applications throughout various markets. From its historical significance to the modern-day technologies in casting methods, aluminum has continuously shown itself as a flexible and useful material. As we browse through the landscape of aluminum casting procedures and look into the ins and outs of quality assurance actions, an extensive introduction of unlocking the real capacity of this steel arises. The possibilities appear countless, encouraging insights that might change the way we utilize and view aluminum in production (casting aluminum).
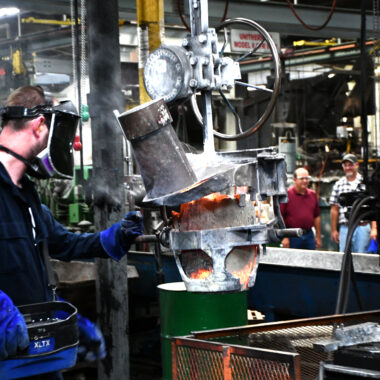
Background of Light Weight Aluminum Casting
Light weight aluminum casting has a rich historical history that dates back to ancient civilizations, showcasing the enduring significance of this metallurgical procedure in numerous industries. The roots of aluminum spreading can be traced to about 5,000 B.C. when ancient human beings like the Egyptians and the Sumerians made use of rudimentary methods to cast little things. Nevertheless, it was not until the 19th century that aluminum casting saw considerable innovations with the discovery of the Hall-Héroult process for drawing out aluminum from its ore, making it extra available for casting purposes.
During the Industrial Revolution, light weight aluminum casting acquired prevalent appeal due to the steel's lightweight buildings and corrosion resistance. This caused its considerable use in making parts for different markets, consisting of automobile, aerospace, and building. The versatility of light weight aluminum casting permitted detailed styles and intricate forms to be generated with precision, additionally sustaining its adoption across various industries. Today, aluminum spreading proceeds to be a cornerstone in the manufacturing of a vast array of products, highlighting its long-lasting legacy and relevance in contemporary production procedures.
Benefits and Applications
With its exceptional strength-to-weight proportion and outstanding thermal conductivity, light weight aluminum casting offers a myriad of benefits and diverse applications across numerous markets. One of the primary advantages of light weight aluminum casting is its light-weight nature, making it an excellent option for sectors where weight reduction is crucial, such as vehicle and aerospace. casting aluminum. Additionally, aluminum casting gives exceptional deterioration resistance, guaranteeing resilience and longevity in extreme settings. Its high thermal conductivity additionally makes it a preferred selection for applications needing warmth dissipation, like in digital components and warmth exchangers.
In regards to applications, light weight aluminum spreading is widely used in the vehicle market for parts like engine blocks, cylinder heads, and wheels as a result of its stamina and lightweight buildings. The building and construction sector gain from light weight aluminum casting in the production of architectural parts and attractive components. The versatility of light weight aluminum spreading prolongs to consumer electronics, where it is made use of in the production of cases and warmth sinks. On the whole, the benefits of light weight aluminum spreading combined with its varied applications make it an essential product in different commercial markets.
Sorts Of Light Weight Aluminum Casting Procedures

Amongst the numerous methods employed in commercial setups, light weight aluminum spreading processes include a variety of methods suited to various applications and needs. Investment spreading, also known as lost-wax casting, is favored for its capacity to generate complex and comprehensive components with a smooth surface finish. Each of these aluminum casting processes supplies one-of-a-kind benefits, catering to a large range of industrial needs.
Innovations in Light Weight Aluminum Casting Strategies
Current improvements in light weight aluminum spreading techniques have reinvented the manufacturing market, offering improved effectiveness and accuracy in the manufacturing of complicated parts. One noteworthy advancement is the development dig this of 3D sand printing innovation, which makes it possible for the creation of intricate sand mold and mildews with marginal manual labor. This method enables for higher layout versatility and faster production cycles, making it ideal for prototyping and little batch production.
Additionally, making use of advanced simulation software program has actually substantially boosted the spreading procedure by making it possible for designers to enhance mold and mildew styles and forecast potential defects before manufacturing starts (casting aluminum). This causes boosted item quality and reduced material waste
Furthermore, the fostering of vacuum-assisted aluminum spreading has actually enhanced the general high quality of castings by minimizing porosity and ensuring a more consistent circulation of molten steel. This technique is especially beneficial for components that call for high structural stability and exceptional surface area coating.
Quality Assurance in Light Weight Aluminum Spreading
The developments in aluminum casting strategies have not just improved efficiency and accuracy however have actually additionally underscored the essential value of top quality control in guaranteeing the dependability and efficiency of actors elements. Quality assurance in aluminum casting involves an organized approach to monitor and review the production procedure, determining any kind of variances from set standards that could influence the end product.
One essential element of quality assurance is using sophisticated technologies such as non-destructive screening techniques like X-ray and ultrasound to identify inner problems without jeopardizing the integrity of the cast components. Furthermore, implementing rigorous assessment procedures at various stages of production aids in recognizing and rectifying problems immediately, ensuring that only components fulfilling the specified criteria are launched for use.
In addition, quality assurance prolongs beyond the production process to include post-casting treatments like heat treatment and surface finishing, assuring that the end products fulfill the wanted requirements. By focusing on quality assurance steps, makers can enhance item consistency, toughness, and general client fulfillment in the world of light weight aluminum spreading.
Final Thought
Finally, light weight aluminum spreading has a rich background and provides numerous benefits and applications throughout various markets. Different kinds of casting processes and ingenious strategies have been developed to enhance the effectiveness and top quality of light weight aluminum casting. Quality control measures play an essential role in guaranteeing the end products fulfill the needed requirements. In general, light weight aluminum spreading remains to be an important manufacturing procedure with great prospective for additional innovations in the future.
As we browse with the landscape of light weight aluminum casting processes and dive into the ins and outs of top quality control actions, a detailed overview of unlocking the real capacity of this steel emerges. It was not till the 19th century that light weight aluminum casting saw significant improvements with the discovery of the Hall-Héroult procedure for drawing out light weight aluminum from its ore, making why not check here it a lot more easily accessible for casting purposes.
Among the different methods employed in commercial setups, aluminum spreading procedures encompass a range of methods matched to various applications and needs. Investment spreading, also understood as lost-wax spreading, is preferred for its capacity to produce in-depth and complex components with a smooth surface area finish. Different types of casting procedures image source and cutting-edge methods have been established to enhance the efficiency and high quality of aluminum spreading.
Report this page